Dd Form 626 Requires Drivers To Provide Which Of The Following
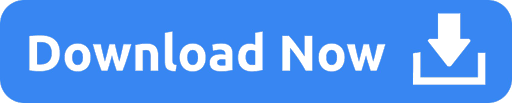
- Dd Form 626 Requires Drivers To Provide Which Of The Following Us
- Dd Form 626 Requires Drivers To Provide Which Of The Following State
- Dd Form 626 Requires Drivers To Provide Which Of The Following Time
- Dd Form 626 Requires Drivers To Provide Which Of The Following Will
Subreddit Rules. 1. Treat other users with respect and civility. Posts must be on topic about UCLA or at least of obvious interest to UCLA students/faculty/staff. 3. Sep 13, 2015 A DD form 626 is a military pre-trip inspection form for vehicles carrying hazardous materials. (HazMat) 1 2. How do you think about the answers? You can sign in to vote the answer. I'm not in NY, but in Texas (which is pretty lax on things) there is no way you would pass. You probably just need to bleed the. Most Viewed News. Descargar Libro Diario De Una Pasion En Pdf; Bodhi Puja Gatha Pdf Download; Albert King Tab Pdf; Dd Form 626 Requires Drivers To Provide Which Of The Following. I have a sears single barrel shotgun i beleive is built by boito. Model number 282510820. Serial number 443449. Can you please help me identify it/.
(a)Criteria for hazardous waste regulation of waste non-chemical military munitions in transportation.
(1) Waste military munitions that are being transported and that exhibit a hazardous waste characteristic or are listed as hazardous waste under 40 CFR part 261, are listed or identified as a hazardous waste (and thus are subject to regulation under 40 CFR parts 260 through 270), unless all the following conditions are met:
(i) The waste military munitions are not chemical agents or chemical munitions;
(ii) The waste military munitions must be transported in accordance with the Department of Defense shipping controls applicable to the transport of military munitions;
(iii) The waste military munitions must be transported from a military owned or operated installation to a military owned or operated treatment, storage, or disposal facility; and
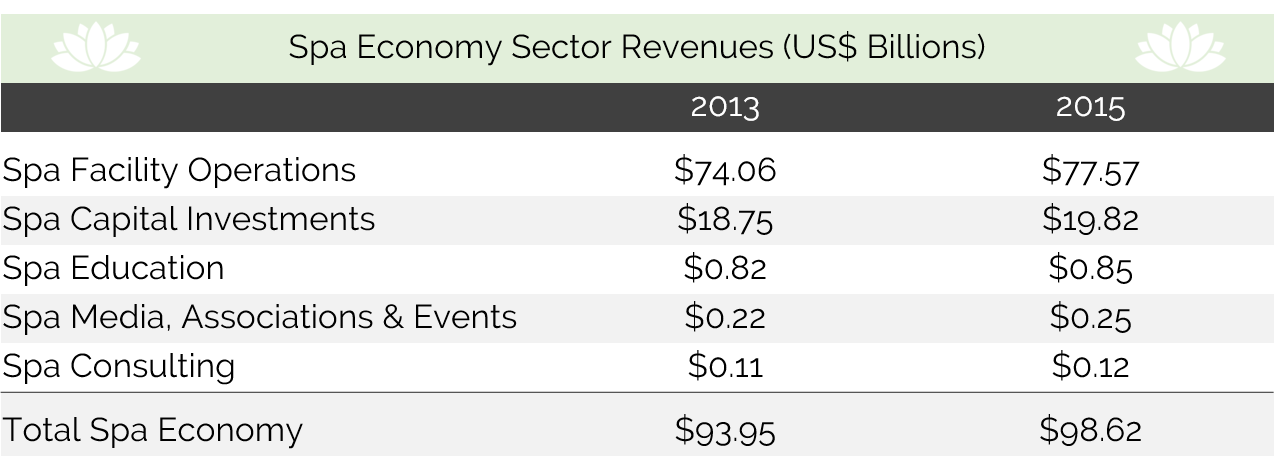
(iv) The transporter of the waste must provide oral notice to the Director within 24 hours from the time the transporter becomes aware of any loss or theft of the waste military munitions, or any failure to meet a condition of paragraph (a)(1) of this section that may endanger health or the environment. In addition, a written submission describing the circumstances shall be provided within 5 days from the time the transporter becomes aware of any loss or theft of the waste military munitions or any failure to meet a condition of paragraph (a)(1) of this section.
(2) If any waste military munitions shipped under paragraph (a)(1) of this section are not received by the receiving facility within 45 days of the day the waste was shipped, the owner or operator of the receiving facility must report this non-receipt to the Director within 5 days.
(3) The exemption in paragraph (a)(1) of this section from regulation as hazardous waste shall apply only to the transportation of non-chemical waste military munitions. It does not affect the regulatory status of waste military munitions as hazardous wastes with regard to storage, treatment or disposal.
(4) The conditional exemption in paragraph (a)(1) of this section applies only so long as all of the conditions in paragraph (a)(1) of this section are met.
(b)Reinstatement of exemption. If any waste military munition loses its exemption under paragraph (a)(1) of this section, an application may be filed with the Director for reinstatement of the exemption from hazardous wastetransportation regulation with respect to such munition as soon as the munition is returned to compliance with the conditions of paragraph (a)(1) of this section. If the Director finds that reinstatement of the exemption is appropriate based on factors such as the transporter's provision of a satisfactory explanation of the circumstances of the violation, or a demonstration that the violations are not likely to recur, the Director may reinstate the exemption under paragraph (a)(1) of this section. If the Director does not take action on the reinstatement application within 60 days after receipt of the application, then reinstatement shall be deemed granted, retroactive to the date of the application. However, the Director may terminate a conditional exemption reinstated by default in the preceding sentence if the Director finds that reinstatement is inappropriate based on factors such as the transporter's failure to provide a satisfactory explanation of the circumstances of the violation, or failure to demonstrate that the violations are not likely to recur. In reinstating the exemption under paragraph (a)(1) of this section, the Director may specify additional conditions as are necessary to ensure and document proper transportation to protect human health and the environment.
(c)Amendments to DOD shipping controls. The Department of Defense shipping controls applicable to the transport of military munitions referenced in paragraph (a)(1)(ii) of this section are Government Bill of Lading (GBL) (GSA Standard Form 1109), requisition tracking form DD Form 1348, the Signature and Talley Record (DD Form 1907), Special Instructions for Motor Vehicle Drivers (DD Form 836), and the Motor Vehicle Inspection Report (DD Form 626) in effect on November 8, 1995, except as provided in the following sentence. Any amendments to the Department of Defense shipping controls shall become effective for purposes of paragraph (a)(1) of this section on the date the Department of Defense publishes notice in the Federal Register that the shipping controls referenced in paragraph (a)(1)(ii) of this section have been amended.
CHAPTER 10
LOADS AND LOADING OPERATIONS
10-1. RESPONSIBILITIES OF UNIT PERSONNEL. All motor transport company personnel have some responsibility for vehicle loads and cargo loading. A discussion of individual responsibilities follows. For specific information on loading, see FM 55-15 or the applicable vehicle technical manual.
a. Company Commander. The company commander develops training plans for the unit. He ensures that company personnel are qualified to safely operate all equipment and are thoroughly trained in the principles of loading, securing, and transporting cargo. He also ensures that company training plans support individual driver skills, the required METL, and MOS training.
b. Platoon Leader. The platoon leader and platoon sergeant develop the platoon's training plans based on their assessment of training needs. Plans include both individual and collective tasks. The platoon leader and platoon sergeant also implement company training plans and policies and ensure that squad leaders are qualified. They review driver testing and qualification records and observe driver training. They keep the commander informed of the platoon's level of training.
c. Truckmaster. The truckmaster maintains driver qualification records and ensures that personnel are properly trained before being licensed. He must be satisfied that training is conducted according to standard. For this reason, the truckmaster regularly observes driver training. Based on the type of equipment in the unit, he may incorporate load and loading criteria in testing. The truckmaster also screens commitments that involve unusual or hazardous loads and highlights them for the tasked platoon.
d. Squad Leader. The squad leader trains drivers to properly load and secure cargo on their vehicles. He ensures that operators know what they are carrying and that both drivers and vehicles are prepared to move the types of loads specified in taskings. The squad leader also supervises maintenance and ensures that vehicles meet operational standards.
e. Driver. The driver supervises the loading of his vehicle and ensures that his cargo is properly loaded and secured against movement. He further ensures that the load is balanced and does not exceed the vehicle capacity as noted on the data plate. He uses the vehicle tarpaulin to protect the load from the weather and pilferage. Once the driver accepts the load from the shipper, he alone is responsible for its safe delivery. The driver should not accept an unsafe load and must resolve any dispute before moving.
10-2. SHIPPER'S RESPONSIBILITIES. Unless the vehicle has an onboard loading system such as a crane or PLS, the shipper normally loads the vehicle. The shipper provides all tie-down devices, dunnage, blocking and bracing materials, and special tools required to secure the load. An exception is loading containers on semitrailers equipped with locking devices. The shipper also prepares shipping documents such as the TCMD.
10-3. CARGO CHARACTERISTICS. The shipper's request for transportation identifies the characteristics of the cargo--its description, dimensions, and weight. This data is used by unit operations personnel to plan the number and types of vehicles needed to support the movement and tells drivers what they need to prepare for the movement (such as the requirement for a tarpaulin, placards, protective clothing, and fire extinguishers). If transporting hazardous material, this information alerts drivers to prepare vehicles for certain inspections and to seek guidance on loading techniques from squad leaders, platoon sergeants, or truckmasters.
a. Cargo Area. The vehicle cargo area is measured in cubic feet. (To calculate cubic feet, take the length times width times height.) Cargo dimensions should not exceed the dimensions of the vehicle. An exception is made for certain outsize loads where there is an overhang from the sides or tail end. To make efficient use of assets, transportation units should try to maximize the weight and cube of vehicles and send only the number of vehicles that can safely carry the load. Theoretically, a perfect cargo load is one that exactly matches the cubic measurement of the vehicle's cargo area and its allowable weight. For example, if the maximum payload capacity of an M923 5-ton cargo truck traveling on a highway was fully used, the load (piled no higher than the side racks) would occupy about 550 cubic feet (15.40 cubic meters) and weigh 20,000 pounds. These conditions are seldom met. The weight, bulk, shape, and compatibility of the cargo, along with road conditions, affect how the vehicle will be loaded.
b. Weight. When loading dense cargo such as ammunition or machinery, the vehicle weight limit may be reached before the cargo space is filled. In other words, it may weigh out before it cubes out. In such cases, the load must be blocked and braced to prevent shifting. With most military cargo loads, however, the vehicle will cube out before it weighs out.
The weight of most military cargo is usually stenciled on the package and noted on the transportation request. The total shipment weight equals the sum of the individual package weights. If the weight is not stenciled on the cargo, the driver should ask the shipper to weigh it before loading. If this is not feasible, the driver should try to have the vehicle weighed after loading. This will ensure that the vehicle is not overloaded.
When these options are not possible, the driver should require the shipper to provide an estimated weight and annotate the estimated weight on the shipping document. If the driver has doubts about the vehicle's ability to transport the load safely, he should not accept the load.
c. Cargo Compatibility. Shippers are required to identify commodities that should not be shipped together on the same vehicle. If there is any doubt and before the driver transports the cargo, shippers should consult appropriate references for guidance. For shipments within CONUS, use 49 CFR, Part 177. When operating overseas, rules of the host country apply. The rules of each country transited, as well as international agreements, govern international shipments of hazardous cargo by highway. If the driver has any doubt about the safety of the load, he should contact the nearest transportation officer, movement control team, or his unit.
10-4. ROAD CONDITIONS. Every road can be classified based on its construction. Engineers normally classify roads. Classification includes bridges, tunnels, and other features that limit width, height, or weight. The payload capacity of a vehicle may be too high for existing roads or bridges. Light surface, loose surface, or fair weather roads may not bear the weight of a fully loaded vehicle. Accordingly, a driver must be familiar with the road he will travel and how its condition affects the allowable payload. For example, an unimproved mountainous road dictates a reduced load compared to a flat hard-surfaced highway. The nature of the road surface may also affect the amount of blocking and bracing needed to secure the load.
10-5. LOADING PROCEDURES. Proper loading procedures are essential to safe operations. They also support successful mission accomplishment by ensuring operational economy and efficiency. Truck unit capability is specified by TOE. See FM 55-15 for vehicle and equipment planning factors and AR 385-55 for more information on requirements for transporting passengers in tactical vehicles.
a. Improper Loading Practices. Underloading and overloading are improper loading practices. Though underloading does not affect vehicle operation or safety, it does affect operational efficiency. Underloading requires more vehicles than necessary to do the job. It wastes vehicles and personnel and causes unnecessary expenditures of fuel and lubricants. It also creates added highway regulation and traffic control problems that can affect all highway movements in the area. Vehicle overloading is a serious concern because it can damage the vehicle and is unsafe. Drivers should not accept loads that are greater than the authorized payload.
b. Loading Cargo. The amount of cargo that can be loaded lengthwise into a truck varies by truck size and model. The length and width of cargo trucks and semitrailer bodies is listed in TB 55-46-1. If it is necessary for pipes, lumber, or other cargo to hang over the front and rear of the vehicle, the cargo must be blocked to keep the weight off the tailgate. A red flag must also be placed at each end of the load in the daytime (a red light at night) to warn other motorists that the vehicle needs added road space. The amount of overhang allowed varies from state to state and country to country. Units must know local traffic rules. The following are general rules for loading cargo:
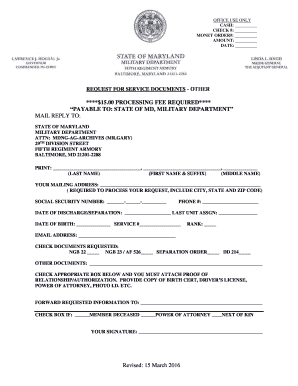
- Place heavy items on the bottom and lighter cargo on top.
- Distribute heavy cargo as evenly as possible over the bed to maintain a safe weight distribution.
- Block and brace cargo with lumber or other materials to keep the load from shifting or falling off the vehicle while en route.
- Keep the load as low as possible. A high load may make the vehicle difficult to control and may cause it to overturn.
- Fill the cargo space of the vehicle to the maximum weight allowable.
- For multistop loads, separate cargo by destination for easy offloading.
- If possible, load items of uniform size and weight together (this simplifies lashing, blocking, and distributing cargo).
- Load drums and barrels either upright or on their sides. If loaded on their sides, their length should be parallel to the sides of the truck (Figure 10-1).
Cacani free download. Figure 10-1. Cargo loading methods
c. Troops and Their Equipment. Certain vehicles designed for cargo may also carry troops and EPWs. The number of troops varies with the size of the truck and duration of the trip. Only authorized individuals may ride in military vehicles. Passengers must stay seated with all parts of their bodies inside the truck. Ventilation must protect them from exhaust gases. They should mount or dismount only after the driver or assistant driver has lowered the tailgate and disconnected the safety strap. If the tactical situation permits, a tarpaulin should be used to protect troops from the weather.
To prevent injury during loading or unloading, a soldier should not mount or dismount the vehicle with his weapon. He should pass it to someone already on board or to the person behind waiting to mount. Each soldier takes back his weapon once on board. Likewise, a soldier should not mount or dismount the vehicle with his truck sack or duffel bag on his back. Once on board, he should stack it on the bed of the truck or under the seats. The number of truck sacks or duffel bags that accompany soldiers will reduce the number of troops that can be loaded on each vehicle. However, loading them with the soldiers also reduces the chance of lost equipment.
Individual equipment not needed on the march may be loaded in separate trucks or trailers. This practice relieves soldiers of added responsibility and is less fatiguing. It also ensures that, if the enemy attacks, soldiers will not be burdened with nonessential equipment. Passengers and cargo are never hauled on the same vehicle.
10-6. TRANSPORTING HAZARDOUS MATERIAL. Hazardous material is a material or substance capable of posing an unreasonable risk to health, safety, and property when transported, as determined by the Secretary of Transportation. Hazardous materials are designated in 49 CFR and include the following:
- Explosives.
- Flammable liquids.
- Flammable solids.
- Oxidizing materials.
- Corrosive liquids.
- Compressed gases.
- Poisons.
- Radioactive material.
- Chemical agents.
- Ammunition.
Trucks hauling passengers will be separated from any vehicle hauling hazardous cargo by at least one buffer vehicle hauling general cargo.
a. References. In CONUS, Army vehicles carrying special loads must comply with 49 CFR and AR 190-11. When operating overseas, local regulations and policies apply. For detailed instructions on hauling AA&E, refer to AR 190-11 and AR 55-355. For information on transporting radioactive materials, see AR 385-11 and TM 55-315. For information on transporting chemical agents, see AR 50-6 and TM 3-250. For information on transporting nuclear weapons and materials, see AR 700-65. For instructions on the handling and storage of hazardous material, see TM 38-410. The proper marking and placement of placards on vehicles carrying hazardous cargo is covered by 49 CFR within CONUS (see 49 CFR, Parts 100-199, or FM 55-15, Appendix E) or by overseas regulations.
b. Shipper Responsibilities. Any shipper who offers a hazardous material for transportation must describe the hazardous material on the shipping documents. The driver of a motor vehicle containing hazardous material must ensure that the shipping document is readily available in the event of an accident or inspection.
At origin, the shipper must inspect vehicles before they are loaded with hazard Classes 1.1 through 1.3 ammunition, explosives, poisons, radioactive 'Yellow III' material, and chemical agents. The shipper uses DD Form 626 (Figure 10-2). Each item on the form must be completed. The driver must correct all deficiencies before the vehicle is loaded.
c. Receiver Responsibilities. If the destination is a restricted area, the vehicle is inspected before unloading using the DD Form 626. A restricted area is any area to which entry is subject to special restrictions or control for security reasons or to safeguard property or material. An example is an ammunition supply point. Deficiencies must be corrected at the time of inspection if practicable and if necessary for safe delivery to the unloading point. If a correction is necessary but impracticable, proper action must be taken to ensure safe delivery of the shipment. This could include use of ground guides, reduced speed, or escort vehicles. Military shippers use DD Form 836 (Figure 10-3,) to instruct drivers transporting hazardous material. The form outlines precautions to take in event of fire, accident, or breakdown. The shipper or transportation officer can add information related to the specific movement. Drivers should get a copy of DD Form 836 from the shipper or ammunition supply point before departure. The driver should read the DD Form 836 before departure and ask questions if he does not understand it.
Figure 10-2. DD Form 626

Figure 10-2. DD Form 626 (continued)
Figure 10-2. DD Form 626 (continued)
d. Loading and Unloading Hazardous Material. General requirements for loading and unloading hazardous material are as follows:
- Ensure the vehicle is safe to operate and free of fire hazards.
- Check to ensure there are no exposed wires.
- Clean off excess oil or grease accumulated on the vehicle.
- Check the fuel system for leaks.
- Set hand brake during loading and unloading and chock the wheels.
- Inspect the load and the vehicle during rest or refueling stops.
- Do not leave the vehicle unattended.
- Do not let anyone loiter near the loaded vehicle.
- Ensure hazardous cargo is marked with the proper shipping name, identification number, and appropriate labels (see 49 CFR).
- Mark the front, sides, and rear of the vehicle with the appropriate placards.
- Ensure the shipper blocked and braced the load to prevent shifting.
Drivers should see their squad leader for information on the loading, blocking, and bracing requirements for hazardous cargo before going to the loading site.
e. Specific Types of Hazardous Material. Besides cargo that requires DD Forms 626 and 836, specific types of hazardous material have other requirements that must be met for transporting. Personnel involved must know and observe current safety regulations and policies contained in AR 55-355, AR 385-10, 49 CFR, as well as in local policies.
Close and secure the tailboard or tailgate. Do not load on the tailgate. | Figure 10-4. Proper loading arrangement for ammunition |
- Consult with officials on the scene before passing by a fire on the road.
- Do not push or tow a truck carrying explosives except to move it off the road.
- Do not transport detonating caps with other explosives. Complete rounds of artillery ammunition, including fuses and primer, can be carried in one vehicle.
- Ensure that artillery shells are laid on their sides. The sides of the projectiles should be parallel with the truck body.
- Follow a planned route that minimizes exposure in densely populated areas. Park in uncongested areas.
- Drive a safe distance away from other traffic.
- Protect cargo against shifting. Do not make sudden stops or turns.
(2) Flammable liquids . The following are special rules for flammable liquids:
- Do not smoke within 25 feet or use open flames within 25 feet during loading, unloading, or transport of the cargo.
- Turn the engine off during loading and unloading.
- Carry two serviceable carbon dioxide or dry chemical fire extinguishers with at least a 10 BC rating and know how to use them.
- Remove tarpaulins. If this is not possible, dry and air tarpaulins that have been saturated with gasoline or fumes before storing them.
- Ensure that electrical connections on petroleum semitrailers and filling apparatus are properly grounded.
- Do not wear hobnail or metal-cleated boots.
(3) Flammable solids and oxidizing materials Special rules for flammable solids and oxidizing materials are as follows:
- Protect the load from adverse weather and keep cargo dry.
- Provide ventilation of the load.
(4) Corrosive liquids . The following special rules apply to corrosive liquids:
- Inspect containers for leaks. Do not load leaking containers.
- Ensure containers are tightly closed (whether full or empty).
- Ensure storage batteries are protected from movement and from contacting each other; protect and insulate the terminals against short circuits.
(5) Compressed gases . The following are special rules for compressed gases:
- FCompressed gases
- Place cylinders on flat surfaces.
- Ensure cylinders are blocked and braced to prevent movement.
- Ensure engine is stopped.
(6) Poisons Do not transport poisons in the same vehicle with food or edible material.
I am new to this forum - couldn't find a better place to ask this question. Thanks in advance for any help. Cakewalk sonar home studio download. I agree, it's got all the improvements that have been made since your version and is only $50. 9.01 seems to work very well, though I wish it had more music notations such as 'repeats', 'DC', etc.
(7) Radioactive materials The ITO has a copy of the Department of Transportation regulations that govern radioactive shipments. Also see TM 55-315 and 49 CFR. The following rules apply to radioactive shipments:
- Ensure that packages containing radioactive materials have yellow or white labels on them IAW 49 CFR.
- Use partitions in cargo compartments to separate yellow labeled packages from people and undeveloped film.
- Base the separation distances on the total transport index shown on the yellow labels. The transport index shows the degree of control the driver must use while transporting the cargo. Add up the transport indexes on all yellow labels. Do not load more than 50 transport indexes on one truck. After all transport indexes have been added, verify the separation distance with the shipper.
- Check the cargo area of the vehicle for protruding nails or bolts.
- Do not transport hazard Class 1.1, 1.2, or 1.5 explosives with radioactive materials.
- Be sure to monitor for radioactivity, if required. If monitoring is required, the shipper must provide the monitoring device and someone skilled in its use.
- Do not transport personnel in the cargo compartment of a vehicle transporting radioactive material.
(8) Chemical agents and chemical ammunition Special rules for chemical shipments are as follows:
- Check the cargo area of the vehicle for protruding nails or bolts.
- Carry individual chemical defense equipment.
- Know proper first aid procedures (see FM 21-11).
- Check the shipper's use of TM 3-250. TM 3-250 has a table that shows chemical agents that cannot be loaded together.
- Know the symptoms produced by escaping toxic chemical agents.
- Wear any protective clothing the shipper provides.
- Do not smoke within 25 feet or use open flames within 25 feet during loading, unloading, or transport of the cargo.
According to AR 50-6, shipments of certain categories of chemical surety material must be accompanied by technical escorts who are qualified by the CPRP.
10-7. OVERSIZE AND OVERWEIGHT LOADS. Civil authorities determine limitations on the weight and dimensions of vehicles using public highways. Consequently, restrictions vary considerably for shipments in the United States and in overseas areas. Unit personnel must know the applicable regulations for the area in which they are operating. During combat operations, the movement control headquarters issues instructions for determining oversize and overweight loads. These limitations are established to prevent damage to MSRs and to allow for safe movement of vehicles.
a. Clearance Permit. The unit or activity planning to move oversize or overweight cargo requests a DD Form 1266 (Figure 10-5). This form furnishes the ITO with complete information on the cargo and vehicles to be used. The ITO requests a special hauling permit from the authorities. Clearance permits for the ARNG and USAR are submitted to the state DMC (see FM 55-1). The requesting unit must furnish the following information to the ITO or DMC:
Apr 21, 2019 Title: Kyoukaisenjou no Horizon. English: Horizon in the Middle of Nowhere. Synonyms: Kyoukai Senjou no Horizon. Japanese: 境界線上のホライゾン. Horizon In The Middle Of Nowhere Episode 1. Horizon In The Middle Of Nowhere Ii Episode 1 English Dub. Status: Completed. Aired: Oct 2, 2011 to Dec 25, 2011. Horizon in the Middle of Nowhere Season 1. Episode 1 Those Lined Up Before the Horizon. English (US) English (UK). Watch or download Horizon in the Middle of Nowhere Episode 1 English Subbed online in high quality. Synopsis: In the far future, humans abandon a devastated Earth and traveled to outer space. However, due to unknown phenomenon that prevents them from traveling into space, humanity returns. Jul 09, 2014 Horizon in the Middle of Nowhere II l dub @animeforever687. 【Horizon in the Middle of Nowhere】 武蔵の双嬢 Battle Scene Edit - Duration. Log Horizon Season 2 - Episode 24. Oct 15, 2011 Watch Horizon in the Middle of Nowhere Season 1 Episode 1, Those Lined Up Before the Horizon, on Crunchyroll. In the far future, history is being relived in the land that was once Japan.
- Type of equipment.
- Gross weight, axle loads, and spacing, height, width, and length.
- Origin and destination of movement.
- Date and time of movement.
- Nature of cargo (within security limitations).
See Appendix N for information regarding military vehicle axle weight distribution formulas and percentages.
b. Clearance Warnings. The sides and rear of oversize cargo must have adequate clearance lights or red flags to warn other traffic.
c. Escort Vehicles. When escort vehicles are required, they either must have warning lights or be driven with vehicle headlights on. When required, the lead vehicle carries a WIDE LOAD FOLLOWS sign on the front. The rear escort vehicle has a WIDE LOAD AHEAD sign on the back.
10-8. CARGO SECURING PROCEDURES. To secure the load for safe delivery to its destination, the shipper must follow procedures to lash and/or block and brace cargo. The shipper is responsible for blocking and bracing a load. However, since the driver must deliver the load safely to its destination, some general rules apply:
- Block crates, boxes, and barrels to keep them from shifting en route.
- Use crib blocking whenever possible. It need not be nailed to the floor or sides if placed tightly against the cargo to reduce damage to the floor and sideboards of the vehicle.
- If a gap exists between pipes or lumber and the end of the trailer, block the load with a gate constructed with 4- by 4-inch boards to prevent it from slipping.
- All lumber used for blocking must be free of knots and strong enough to provide a rigid and stable support for the load en route.
- When the load must be protected from the weather, pad the corners of boxes or crates to prevent damage to the tarpaulin.
10-9. DOUBLE-STACKING TRAILERS. Problems may arise when stacking one trailer onto another for transport, especially if loading facilities or equipment (such as ramps, loading docks, and gantry cranes) are available. Several methods can be used to solve these problems. When semitrailers are stacked and shipped as cargo or moved as a matter of convenience, be sure to coordinate with the receiving authority to ensure that the shipment can be unloaded. Experienced drivers should be used when tractors are positioning semitrailers onto or removing them from other semitrailers.
Figure 10-5. DD Form 1266 (front)

The methods described herein are not all-inclusive or restrictive. Based on the personnel, equipment, and facilities available--as well as on the skill and ingenuity of personnel engaged in the operation--units in the field may devise other methods or variations of the methods discussed here.
Procedures can be combined by using one loading method at origin and a different unloading method at destination. Consider the options when planning and conducting an assigned transport mission.
a. Flip Method. The flip method loads one semitrailer onto the other in a bed-to-bed position (Figure 10-6). This method requires no special facilities and can be done using a unit recovery vehicle or other lifting device.
Dd Form 626 Requires Drivers To Provide Which Of The Following Us
The two semitrailers ride bed-to-bed. The top semitrailer is secured on the cargo bed of the transporting semitrailer using chains, wire, rope, or banding devices for tie down. The transporting tractor-semitrailer unit should rest on as level and compact a surface as possible during loading and unloading. This is essential to prevent accidents, personal injury, damage to equipment, and delays. When the transporting semitrailer is not hooked up to a tractor during loading operations, ensure that the surface on which the landing gear rests is firm. If necessary to prevent the landing gear legs from sinking into the ground, strengthen and reinforce the ground surface using fill, gravel, lumber or timbers, pierced steel planking, or other suitable materials. Block the wheels of the bottom semitrailer and set the brakes to prevent movement.
The flip method loading procedure is as follows:
| Figure 10-6. Flip method used for loading semitrailers |
To unload the semitrailer at destination, reverse the loading steps:
- Remove all tie-downs and unload the side and end boards.
- Attach side rail tie-downs and use a recovery vehicle or other lifting device to lift and flip the semitrailer back onto the ground. Then remove the side rail tie-downs.
- Extend the landing gear after the rear wheels of the semitrailer rest on the ground. Use the recovery vehicle to hold the load until the gear is extended.
Field reports indicate that the following problems may occur when using this method:
- Side rails and marker lights on both semitrailers may be damaged during flipping.
- Semitrailer brake fluid may leak through the master cylinder vent.
- Landing gear may lose hydraulic fluid due to the semitrailer resting in an upside-down position.
Use care during loading and unloading to minimize damage. After delivery, both semitrailers will be inspected and serviced and/or repaired before being put back into service. A variation of the flip method is one in which the semitrailer is first flipped over to rest on its bed on the ground. Two recovery vehicles at each end (one set off to the side) then lift and hold this semitrailer while the transporting semitrailer is maneuvered under it. Then, the top semitrailer is lowered into place.
In the lifting, portable ramp, and terrain features methods, the top semitrailer rests in an upright position (on its wheels and landing gear) on the bed of the other semitrailer. It must not only be tied down but must also be securely blocked and braced.
b. Lifting Method. The lifting method loads the top semitrailer in an upright position (Figure 10-7). It requires no facilities and can be performed using one tractor and the unit recovery vehicle (or other suitable lifting device). The loading procedure is as follows:
- Back the transporting semitrailer up to the rear of the transported semitrailer.
- Use the recovery vehicle to lift the transported semitrailer by the rear lifting shackles.
- Back the transporting semitrailer approximately halfway under the lifted semitrailer. Lower the semitrailer onto the cargo bed of the other semitrailer.
- Shift the recovery vehicle to the front end of the top semitrailer and, using the front lifting shackles, lift the front end.
- Hold and maneuver the transported semitrailer with the recovery vehicle boom while the transporting semitrailer is backed into proper position under the load. Lower the semitrailer onto the cargo bed of the transporting semitrailer.
- Block, brace, and tie down the semitrailer; load and secure side and end boards.
If two recovery vehicles or lifting devices are available, they may be positioned at each end of the transported semitrailer (one set off to the side) to lift and hold that semitrailer while the transporting semitrailer is maneuvered and backed under it. The transported semitrailer is then lowered into position.
To unload the semitrailer at destination using the same method, reverse the loading steps as follows:
| Figure 10-7. Lifting method used for loading |
c. Portable Ramp Method. This method requires making a portable ramp (mounted on skids, rollers, or wheels) for use in the loading process (Figure 10-8). The loading procedure is as follows:
- Position the ramp at the rear of the transporting semitrailer.
- Use a tractor to back the transported semitrailer up the ramp and onto the transporting semitrailer. Extend the landing gear, uncouple, and remove the tractor.
- Block, brace, and tie down the semitrailer. Load and secure the side and end boards.
To unload the semitrailer at the destination using this same method, reverse the loading steps as follows:
Instruction contained in the loading caution apply as well to the unloading. |
- Place the portable ramp in position at the rear of the transporting semitrailer.
- Remove the tie-downs and blocking and bracing. Unload the side and end boards.
- Back the towing tractor into position and up the ramp. Hook up and tow the semitrailer from the transporting semitrailer.
- Install (or load) the side and end boards. Move the semitrailer out.
Figure 10-8. Portable ramp used for loading semitrailers
d. Fixed Ramp Method. The fixed ramp method is similar to the portable ramp method (Figure 10-9). In this instance, the ramp used is an immovable field expedient type, and the transporting semitrailer must be backed into position at the ramp for loading.
The fixed ramp is prepared using heavy timbers, railroad ties, or impacted earth. The timbers or ties should be spiked, bolted, or otherwise secured together. Tamp the earthen ramp firmly and then surface it with planks, pierced steel planking, or other available materials to make a firm, solid surface. Shore the earthen ramp at the loading end to prevent breakdown during its use. The loading procedure is as follows:
- Back the transporting semitrailer into position at the ramp.
- Back the semitrailer to be transported up the ramp and into position on the bed of the transporting semitrailer. Extend the landing gear, uncouple, and remove the tractor.
- Block, brace, and tie down the transported semitrailer. Load and secure the side and end boards.
To unload the semitrailer at the destination using a tow-off method, either a portable or fixed ramp or other similar facility may be used. If a portable ramp is used, the procedures for the portable ramp method apply. If a fixed ramp or facility is used, procedures for the fixed ramp method apply.
Dd Form 626 Requires Drivers To Provide Which Of The Following State
Figure 10-9. Fixed ramp used for loading semitrailers
e. Use of Terrain Features. Natural or manmade terrain features (arroyos, dry river beds, natural land depressions, cuts and fills, ditches, trenches, and so forth) may be used or adapted for use as loading ramps (Figure 10-10). Based on the contours of the feature used, either little or no pioneer work or extensive work may be required to prepare it for operations.
Figure 10-10 (a) shows a cross section of a terrain feature. The heavily shaded area (b) illustrates where earth removal is required to make it a suitable ramp; (c) illustrates the feature after it is prepared. Note that the face of the cut has been shored to prevent breakdown during use. The loading procedure (d) generally follows the procedures for ramp loading stated earlier.
Unloading the transported semitrailer at destination depends on the facilities available at that point. The semitrailer can be unloaded by any of the methods outlined above, or it may be unloaded using a terrain feature.
Figure 10-10. Use of terrain features for loading semitrailers
Join the GlobalSecurity.org mailing list |
Dd Form 626 Requires Drivers To Provide Which Of The Following Time
Dd Form 626 Requires Drivers To Provide Which Of The Following Will
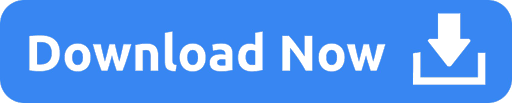